After working a decade in substantial reconstruction of existing homes and commercial buildings I had a lot of good insights into why buildings failed or endured over time, and how the materials and structure of a building interacted with the lives and behaviors of the occupants. Working for not-for-profit housing developers, I became interested in the construction of new homes that were affordable, durable and efficient, what today we call “sustainable.” With a desire to try some innovative approaches with new technologies, I started a general contracting company in 1986.
Structural Insulated Panels (SIP) were just coming into the market, and our first SIPs project was the Murray Lake House. This custom-built small retirement home was a K. VanDyke design/build project, and was constructed on the foundation of a former summer cottage, on a hill overlooking the lake.
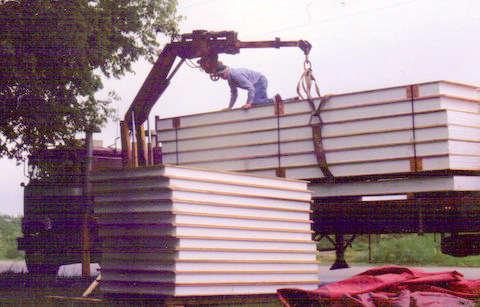
The Joan Avenue House, also a K. VanDyke design/build, was another SIPs project, constructed in 1987. Photos of SIPs being used in the construction of this home are shown below.
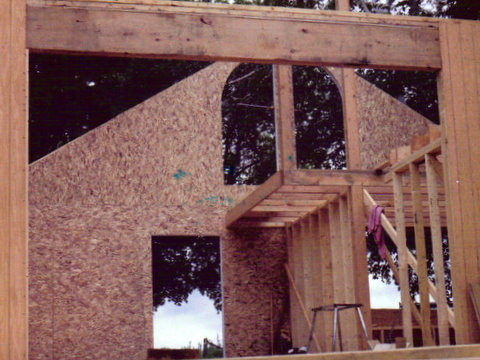
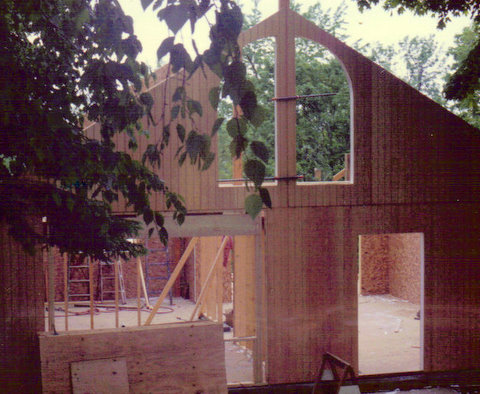
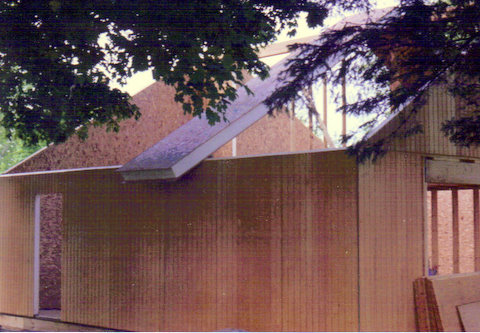
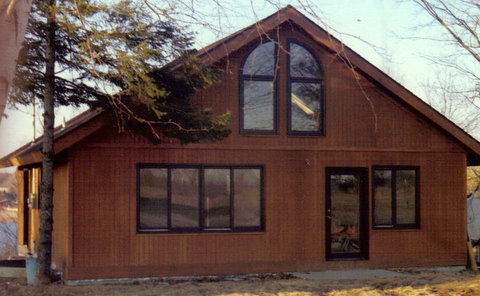
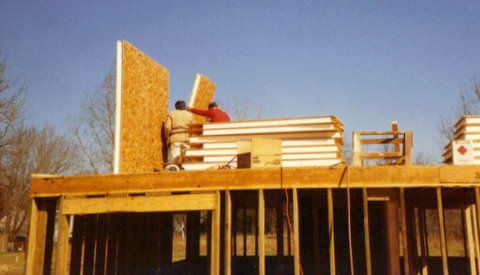
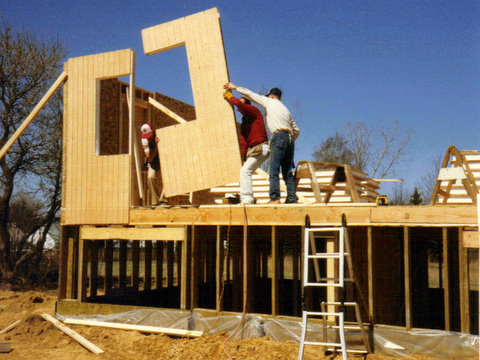
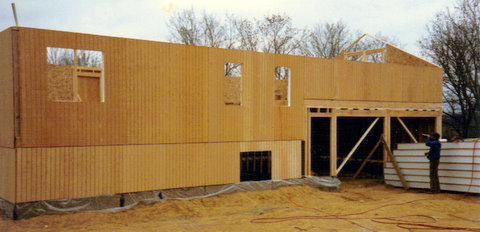
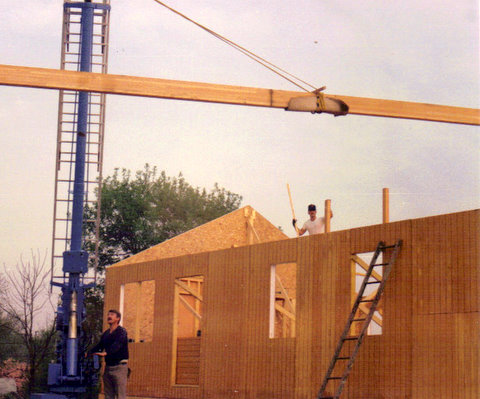
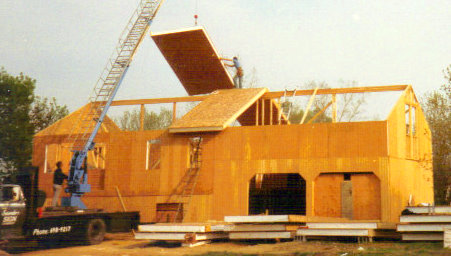
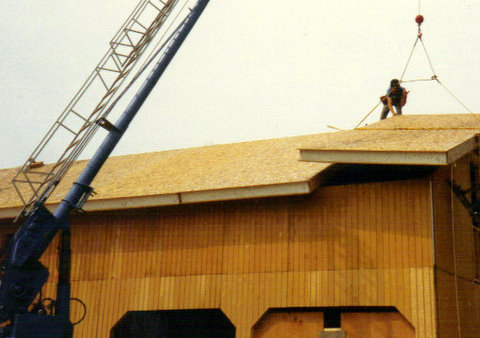
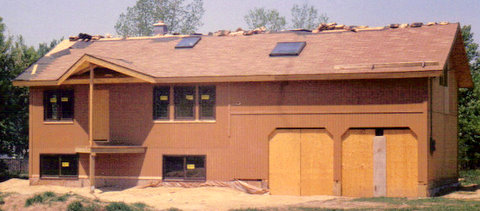

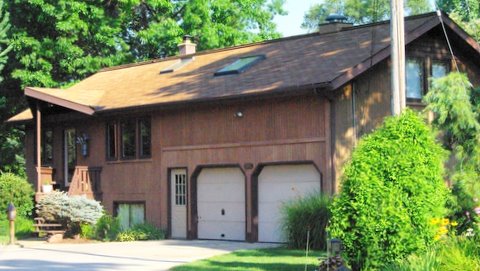
A Pressured-treated Wood Foundation,(PWF) was used for the Joan Avenue House, because the lower level was designed to be living space. It was clear from the outset that an empty, poorly insulated basement has no place in our residential design perspective; we believe that the below-grade portion of every home should be as habitable and well-insulated as the rest of the home. This approach reduces the home’s overall footprint and cost per square foot of living space. A Pressure-treated Wood Foundation was also used for the Springdale House, and other projects.
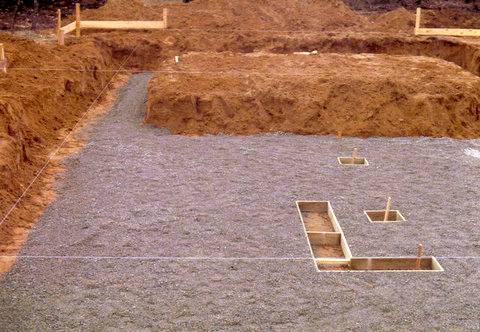
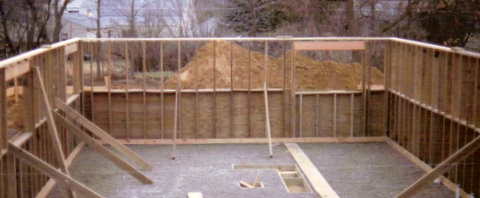

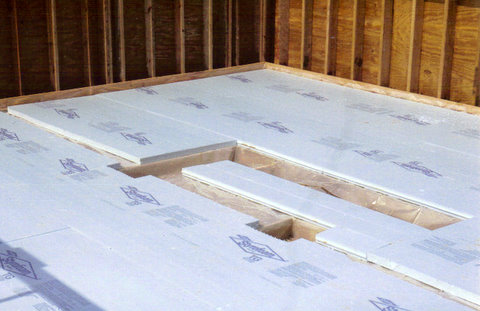

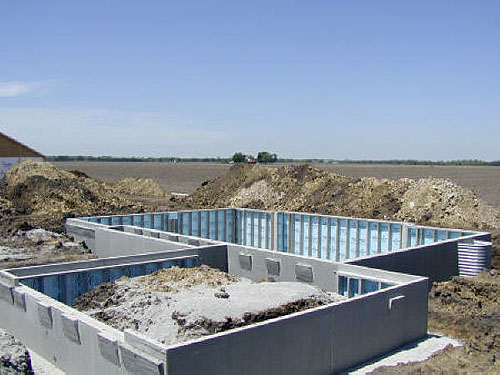
In 1987 Insulated Concrete Forms (ICF) were introduced to our local market, and we did a residential addition with them late that year. We built our first ICF home foundation in 1988 doing all the work with our crew as there were yet no concrete contractors experienced with the product. Today there are a wide variety of ICF products available and we use contractors we specialize in this construction.
Developed in the early 1980’s and introduced to our market area in 1997, Precast Insulated Concrete walls (PIC), use a crushed stone base similar to that of a wood foundation system. These walls come with an R-5 insulation value and are set up so that adding additional insulation, wiring, plumbing, and drywall finish can all be done with standard field techniques. This foundation system is manufactured and installed locally by Great Lakes Superior Walls Systems. This is system is another very attractive option for foundations, especially when time or working space is limited. We have used these in both single-family and multi-family residential construction. (See www.greatlakessuperiorwalls.com)